Искровое плазменное спекание
Искровое плазменное спекания представляет собой наиболее новым методом и технологией в порошковой металлургии с точки зрения создания и получения новых типов композиционных материалов из наноразмерной керамики и порошков. На рисунке показана классификация методов порошкового спекания существующих в промышленности. Искровое плазменное спекание относится к классу спекания под давлением.
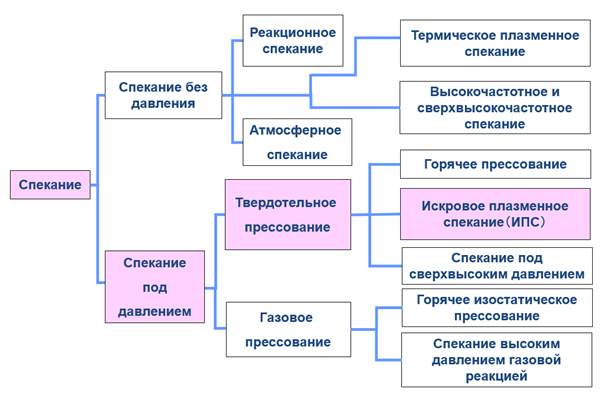
В качестве примера, ниже показана таблица сравнения и преимущества метода искрового плазменного спекания и горячего прессования.
Искровое плазменное спекание | Горячее прессование | ||
---|---|---|---|
Температурный градиент спекания | ◎ | × | |
Контроль спекание границ частиц | ◎ | × | |
Контроль спекание тонкокристаллической структуры | ◎ | × | |
Скорость повышения температур | ◎ | × | |
Время спекания | Скорость повышения температур | Быстро | Медленно |
Время выдержки | Короткое | Долгое | |
Гомогенное спекание | ○ | ○ | |
Возможность расширения | ◎ | △ | |
Производительность | ◎ | △ | |
Инвестиционноеоборудование | ○ | △ | |
Эксплуатационные расходы | ◎ | △ |
На рисунке показана базовая конфигурация системы ИПС. Порошок упаковывается в матрицу и устанавливается между верхним и нижним электродами внутри вакуумной камеры. Затем одноосное давление прикладывается к материалу с помощью верхнего и нижнего пуансона в пресс-форме, а нагрев осуществляется за счет непосредственного протекания импульсов постоянного тока через материал, пуансоны и пресс-форму. При таком подходе возможно получить очень высокие скорости температурного спекания до 2500°С в течение короткого промежутка времени в сравнении с традиционными системами.
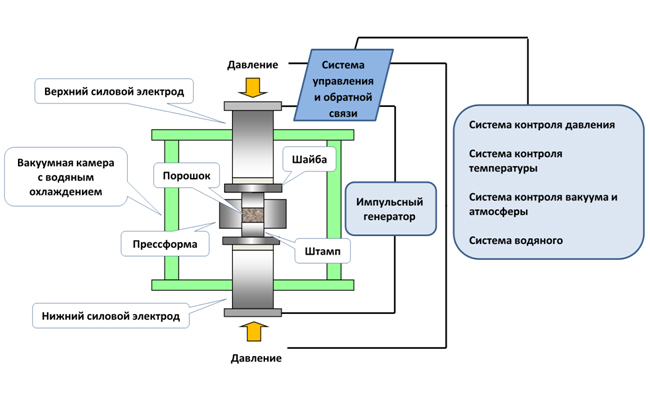
Импульсный ток производит электрический разряд в пространстве между частицами спекаемого материала, что приводит к возникновению искры и моментальному локальному образованию плазмы с температурами до тысяч Кельвина. Такие температуры приводят к оплавлению и испарению материала с поверхностей частиц и способствуют массопереносу и спеканию материала. Процесс может проводится в вакуумной камере или инертной атмосфере.
![]() |
1. Испарение и затвердевание 2. Объемная диффузия 3. Поверхностная диффузия 4. Зерно-граничная диффузия |
РЭМ изображение формирование шейки при спекании | ||||
![]() |
![]() |
![]() |
![]() |
![]() |
Начальная стадия формирования шейки | Уширение шейки | Начала пластической деформации | Формирование шейки после ИПС | Формирование шейки после традиционного спекания |
Тип материала | Материалы для спекания | |
---|---|---|
Металлы | Fe, Cu, Al, Au, Ag, Ni, Cr, Mo, Sn, Ti, W, Be или практически любой металл | |
Керамика | Оксиды | Al2O3, Mullite, ZrO2, MgO, SiO2, TiO2, HfO2 |
Карбиды | SiC, B4C, TaC, TiC, WC, ZrC, VC | |
Нитриды | Si3N4, TaN, TiN, AlN, ZrN, VN | |
Бориды | TiB2, HfB2, LaB6, ZrB2, VB2 | |
Фториды | LiF, CaF2, MgF2 | |
Металлокерамика | Si3N4+Ni, Al2O3+Ni, ZrO2+Ni, Al2O3+TiC, SUS+ZrO2, Al2O3+SUS, SUS+WC/Co, BN+Fe, WC+Co+Fe | |
Интерметаллические соединения | TAl, MoSi2, Si3Zr5, NiAl, NbCo, NbAl, LaBaCuSO4, Sm2Co17 | |
Другие материалы | Органические материалы (полиамиды и др.), композитные материалы |